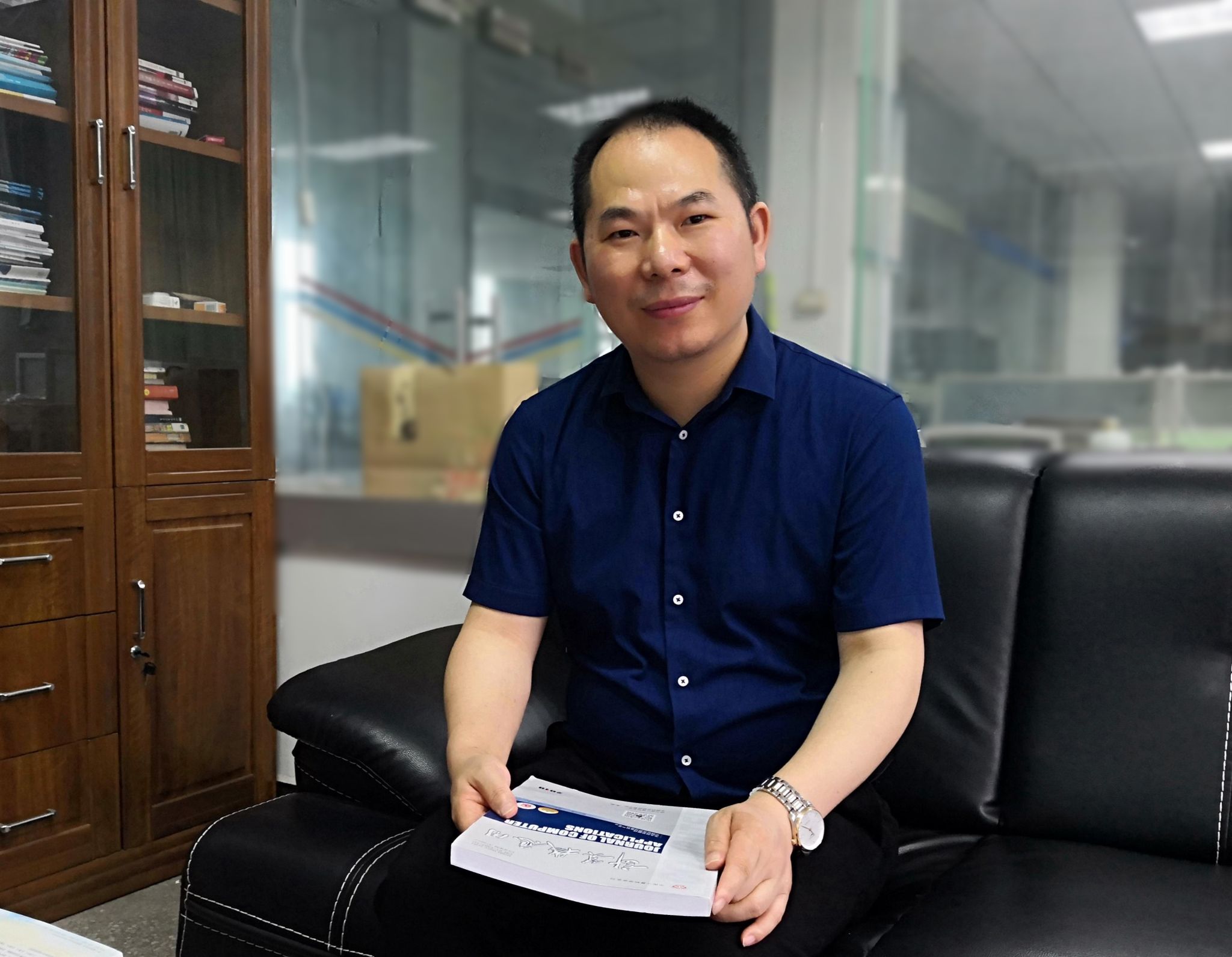
记者 宋钦
李维刚,我校人工智能与自动化学院教授、博士生导师、冶金自动化与检测技术教育部工程研究中心主任,主要从事工业过程控制与检测、人工智能与机器学习算法、机器人定位与导航研究、三维机器视觉研究。
在国内外核心期刊发表论文80余篇,授权中国/美国发明专利30余项,承担并完成国家自然科学基金面上项目、省揭榜制科技项目、省重点研发计划及校企联合研发课题30余项,成果在中国宝武集团等多家大型央企应用。
晚上九点,在信息学院的办公室里,李维刚教授接完电话,继续伏案于项目之中。他是湖北高层次人才入选者、湖北省科技进步一等奖获得者。这样的工作日常,在过去的十九年中发生了无数次。
参与宝钢首条自主集成热连轧线
回想科研生涯,李维刚感慨万千。在中国宝武集团中央研究院工作时,他作为核心研发人员,承担了宝钢首条自主集成热连轧线1880的过程控制系统研发。
当时,核心技术的攻克重担落在仅有30岁的李维刚肩上。该项目耗时五年多,他负责其中关键的轧线模型开发技术。1880项目工艺负责人将该系统列为1880的三大核心特点之一,并称赞这让宝钢热轧首次具备了过程控制计算机系统(L2)与模型的自主开发集成能力。
项目调试期间,工作室温度高达30多度,待一会儿便大汗淋漓,而李维刚一待便是十几个小时。“我们的工作是国内首次研发,没有参考文献,没有指导老师。再困难的问题也要靠自己解决,必须咬牙坚持。”李维刚说。
有一天凌晨5点,李维刚被同事摇醒,让他立即去现场排查问题。当时,工厂正在精轧废钢,生产被迫暂停,大家都不知道问题出在哪。“压力很大,所有人都等着你,不解决问题就不能开工,废钢一块、停产一小时就会带来几十万的损失。”在莫大的压力下,豆大的汗珠从李维刚脸上落下。面对难题,他心里不断默念:“坚持,再坚持。”经过细致缜密的计算与分析,他成功地找出问题根源,并迅速给出解决方案,使生产恢复正常。
经此一事,只要现场有疑难故障,领导、同事第一时间想到的就是李维刚。有时遇上节假日,一接到电话,过会儿他的身影就出现在厂里。
李维刚深切体会到,核心技术决定整个项目的成败,担任了这个角色就要承担起责任。“1880的项目让我受益匪浅,我获得很大成长,之后面对生产问题排查、模型故障诊断、数据分析等,处理起来我都得心应手。”
八年自研攻克热轧难题
在宝武工作几年后,面对热轧技术向“以热代冷”和“高强减薄”发展的趋势,李维刚敏锐地洞察到,市场对超薄、高强、高表面热轧商品材的新需求。
然而,在不改变现有常规热连轧机组装备的情况下,实现高强、超薄规格与高表面质量三者兼备的高附加值产品的规模化生产并非易事。
“超薄”“高强”均会导致精轧机架轧制负荷大,而“高表面”则要求轧制负荷不能过大。上述需求相互矛盾,难以兼顾,轧制难度极大。仅超薄规格的热连轧过程,李维刚将其形象比喻为“一根线连续穿过七个针眼”,任一环节出现些许偏差,带钢就会变成废品。
为了解决这些问题,李维刚一干就是八年。就在他苦苦探索时,人工智能的崛起让他看见了新方向。他发现,通过构建“机理模型+特征点+拟插值+自适应”的全新轧制模型体系,可以实现模型自学习系数的连续化,成功解决换规格轧制模型精度差的难题。
有了合适的“线”,李维刚开始研发能够穿线的“手”和“眼”。他带领团队研发了一套轧机设备精度及操作行为智能辨识系统,能对设备精度进行在线诊断,确保精度失效得到及时预防,同时分析操作行为的有效性并修正操作失误。这一套组合拳打下去,实现了“一根线连续穿过七个针眼”。
国家冶金自动化工程技术中心主任孙彦广评价说,该成果实现了极限规格、极限性能产品的批量稳定生产,“以热带冷”的热轧酸洗产品还节约了大量资源和能源消耗。
该创新成果在中国宝武集团等多家企业迅速推广应用,创造了巨大的经济社会效益。仅梅山钢铁一条热轧生产线,就新增经济效益2.7亿元。
让工业拥有更先进的“中国眼”
离开生产一线来到武汉科技大学后,李维刚仍在关注生产线上的问题。
“我国是钢铁大国,热轧商品材料占据重要地位。但在带钢热连轧中,常出现麻点、夹杂、刮伤等缺陷,影响产品性能。”李维刚介绍,表面检测系统对控制质量、降低废品率至关重要,很长一段时间里,这项技术基本依赖于进口国外成果。
武钢CSP热连轧机组原用德国传统表面检测系统,检出率85%,分类准确率80%,无法满足生产需求。了解到李维刚研发的轧机设备精度及操作行为智能辨识系统后,武钢找上门来寻求改善方案。
“又是一个自研难题!”李维刚感觉充满了动力。他到达武钢,走完整个生产线,仔细观察系统运行,迅速发现了其中的问题:传统的图像识别,仅仅是将拍摄的图片与模板库中已有的图片进行比对,需要人工设计图像特征,这直接导致最终缺陷分类精度的受限。
外国人做的就一定好用且难以改善?李维刚不这么认为。怀着一股冲劲,他带领团队开始攻关。根据已有经验,李维刚决定在现有表面缺陷检测设备的基础上研发一个并行系统,利用深度学习方法开发CSP热轧带钢表面缺陷检测模型,并配套新的表面缺陷检测系统软件。他要在不改变原有基础设备的情况下,“完善”德国的原有系统,实现自研系统的优越性。
科研不是一帆风顺,李维刚碰到了新的难题:实际生产对检测系统的实时性要求特别高,每张照片的处理速度直接关系到系统能否成功上线运行。然而,最初采用的ResNet50模型虽然分类精度高,但模型计算耗时长,这显然不符合实际生产的需求。
“怎样得到精度高但是运算耗时短的模型呢?”带着这一问题,李维刚开始探索和尝试。他经常工作到深夜,咖啡热了一次又一次。在查阅了大量相关论文后,一篇关于“知识蒸馏”的论文让他眼前一亮。“就是这个技术了!”一激动,手边的咖啡差点被打翻。
他仔细阅读了这篇论文,借鉴知识蒸馏的原理,将复杂的ResNet50模型视为“老师”,而简单的LDS-ResNet14模型则作为“学生”。通过提炼和压缩“老师”的知识,再将其传授给“学生”,从而得到一个既处理精度高又处理速度快的新型模型——LDS-ResNet14。
这个项目,李维刚前后耗时近3年。系统上线运行测试的那一段日子里,他时刻关注着。实际现场在线应用结果令李维刚欣喜不已。针对武钢CSP热连轧机组的折叠、油污、夹杂和麻点等四类缺陷,该模型的缺陷检出率高达96.43%,缺陷识别率达到94.10%,满足了实际生产的要求。
经过多年的努力,李维刚带领团队还完成了“3D SLAM移动测图与三维重建系统开发及其在智能机器人与机器视觉中的应用”“室内移动机器人的精准定位与导航关键技术研究”“基于点云模型的机器人自主作业关键技术开发”“平安电工云母板生产线自动剪切系统”等数十项企业横向课题,解决了企业实际生产的技术难题。
“看到生产线上,被国外技术卡脖子和偶发的安全问题都让我心疼不已。”李维刚说,“给机器人、生产线装上我们自己研究的‘智慧眼’,不受制于外人,减少企业安全生产问题,降低产业工人工伤概率,这些是我前行的不懈动力。”